The rise of the machines: tech revolution in the East and global transformation
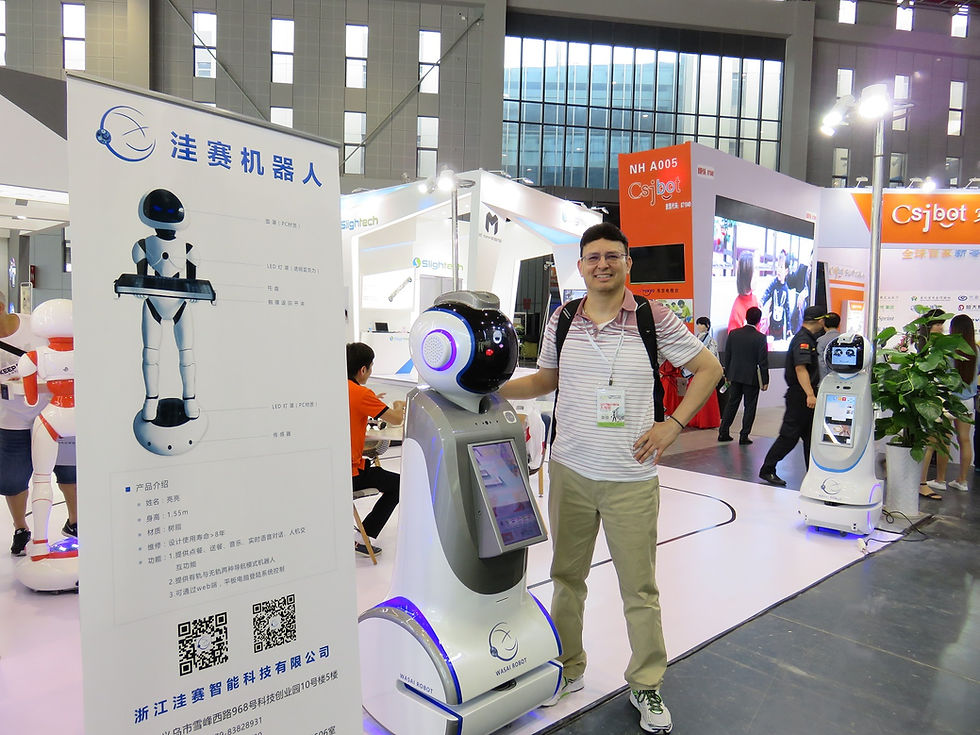
Attending a Chinese robotics exhibition, we can find not only big companies and global players, but, most noteworthy, a myriad of Chinese start-ups. This reflects a profound industrial transformation underway in China. The use of industrial robots has been accelerating around the globe, as they become more affordable and capable. However, they are starting to disrupt the stereotypical image of China’s labor-intensive factories. For instance, E-Deodar Robot Equipment, a subsidiary of Shanghai’s machinery producer Ningbo Techmation, has created a Silicon Valley-style work environment in its factory that resembles the offices of high tech start-ups, with open floor concept, hang-out areas, and robots serving coffee to employees. China has been an important market for industrial robots for a few years, but the International Federation of Robotics estimates that it will soon account for more than one third of industrial robots installed worldwide and be the world’s biggest operator.

Economics and competitive factors are driving this technological transformation across manufacturing and supply networks. There has been a rapid change in the Chinese labor force caused by a decrease in the working-age population, an increase in college enrollments, and a growing middle class. These economic factors have contributed to the rising wages and have challenged the local government and companies. To remain competitive, manufacturers are investing heavily in automation. For instance, the Changying Precision Technology Company factory located in Dongguan, Guandong, has automated production lines, replacing about 90% of its labor force with robots. All the processes are operated by computer-controlled robots, autonomous transport trucks, and automated warehouse equipment.
The government has also been promoting automation to tackle the critical economic challenges of a shrinking and more expensive labor force. However, China is not just sourcing robots from overseas suppliers. A strategic plan titled “made in China 2025” calls for 50% of the national robots’ requirements to be sourced domestically by 2025. This industrial strategy is designed not only to improve the technological capabilities of China’s factories, but also to support the development of Chinese brands globally. The broader strategic goal is to lead emerging markets for artificial intelligence, driver-less vehicles, and digitally-connected appliances.
While China has been one the world’s largest producers of industrial robots, there remains a gap between China’s robotics industry and the top global companies from Europe and the U.S. Most of the industrial robots that Chinese manufacturers purchase for their own use come from abroad and most robots made in China still rely on components sourced internationally. However, this is changing rapidly. For instance, the start-up E-Deodar Robot Equipment has already mastered the critical fundamentals to developing sophisticated robotics: servomotors, drivers, and control panels technology. Other Chinese companies are closing the gap through acquisitions. For instance, Chinese home-appliance maker Midea Group entered the robotics market by acquiring German industrial robotics leader Kuka AG.

Technological developments and the growing volume of e-commerce are also transforming China’s logistics. Similar to some of their counterparts in the U.S., some Chinese managers see a greater opportunity in integrating manufacturing robots with real-time data from customers and automated logistic systems. While Amazon led the pack purchasing Kiva in 2012, JD.com is now investing heavily on automation and digitization. For instance, it is actively testing robots to deliver packages in urban areas and drones to deliver in rural areas. It has set up an augmented reality lab and plans to use the technology to its logistics business and to manage inventory. Alibaba’s Cainiao Network has built its E.T Logistics Lab where it is working on augmented reality (AR). AR glasses can be used to help guide workers through the warehouse by allowing them to read information on parcels. Cainiao Network is developing its Xiao G delivery robot, which can load 10 to 20 parcels from nearby distribution centers and select the best routes to deliver the packages.
In terms of automation in the retail end of supply networks, Alibaba has just launched TaoCafe - below is the first site opened a few days ago in Hangzhou.

While somewhat similar in overall business concept to its U.S. peer AmazonGo, TaoCafe uses a different technological solution and setup to detected whether an item has been picked up - see video below.
Another example that became notorious recently is the “little orange“robots from Shentong Express, a delivery company in Hangzhou, Zhejiang province. The bots, officially known as the Hikvision intelligent sorting robots, can sort up to 200,000 packages a day and are self-charging, like but way more capable that the beloved iRobots we use domestically to clean our homes.
Increased quality requirements, more stringent safety standards and attention to sustainability have driven China towards greater innovation. Right now, the Chinese robotics market is in the growth stage and has attracted many players, including a flourishing number of local start-ups. However, massive investments, strong interest in higher quality and productivity, and lower operating costs through automation will likely consolidate the playing field. Eventually, this will produce a few large and globally competitive robotics powerhouses.
China’s technological transformation will likely change the global manufacturing and supply network landscape. Different from the traditional economic development path, where companies send abroad portions of their value chains to balance high-cost labor and low-cost manufacturing, it is interesting to note that, as its economy continues to modernize, China appears to be automating jobs that would normally be relocated abroad to less developed economies.

As China and other industrial leaders continue to develop more and better robots, the scope of work they can handle will be further expanded. The payback period is consistently diminishing, putting robotics within reach of smaller manufacturers and logistic companies. This challenges us to reflect on their impact on many fronts. For one, advances in robotics and automation will very likely displace low-skilled jobs. However, new positions will be created, but without better education and more skills, workers will struggle to take advantage of advancements in manufacturing and supply chain. The labor force will need, for instance, to be trained in artificial intelligence, machine learning, and robotics. Not only low-skilled jobs will disappear, but there will likely be fundamental changes in the nature of jobs in general in manufacturing and supply chain.